Understanding Vacuum System Components for Optimal Performance
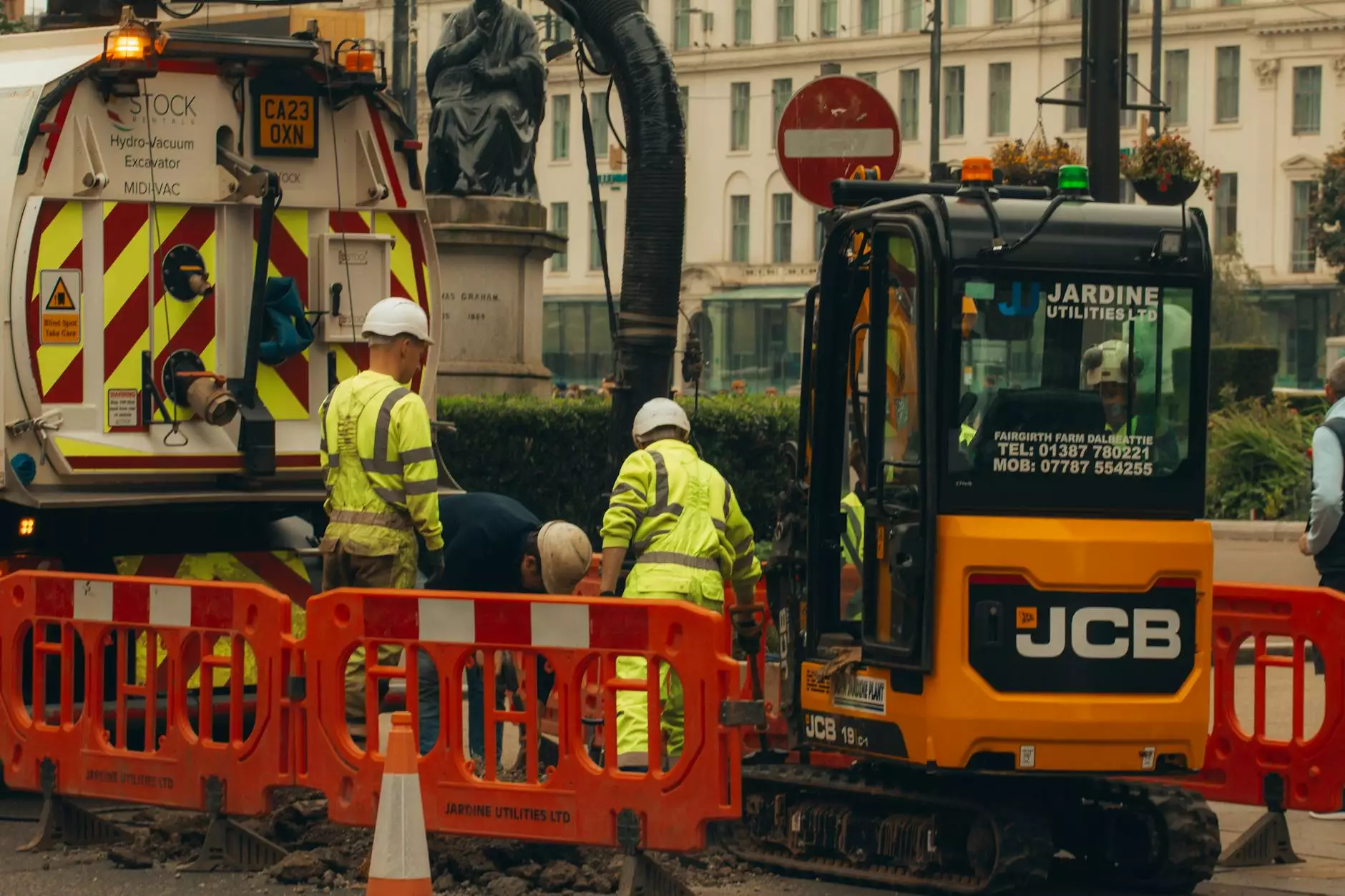
The significance of vacuum system components cannot be understated in today’s technologically driven world. Every industry, from manufacturing to food preservation, depends heavily on these systems for various applications. This article will explore the different components of vacuum systems, their functions, and how they contribute to enhancing operational efficiency in businesses.
1. What Are Vacuum Systems?
At its core, a vacuum system is designed to create and maintain a vacuum—an area devoid of matter. This is achieved through the removal of air or other gases from a sealed environment. These systems are integral across multiple sectors, as they facilitate processes that require a lack of atmospheric pressure. Understanding these systems and their components is crucial for businesses aiming to optimize their operations.
2. The Key Components of Vacuum Systems
The efficiency of a vacuum system hinges on its components. Below, we delve into the primary parts that constitute these systems:
2.1 Vacuum Pumps
One of the most critical components is the vacuum pump. This device removes air and gases from a sealed volume, creating a vacuum. There are various types of vacuum pumps, each suited for different applications:
- Positive Displacement Pumps: These are ideal for achieving high vacuums and are commonly used in laboratory settings.
- Kinetic Pumps: These work by transferring energy to the gas molecules, making them suitable for processes requiring rapid evacuation.
- Captive Pumps: Often utilized in industrial applications, these pumps contain gases and particulates for enhanced environmental control.
2.2 Vacuum Chambers
The vacuum chamber is the heart of any vacuum system. It is the space where the vacuum is created and maintained. Various materials can be used to construct these chambers, and the choice often depends on the specific application. Common features include:
- Sealed Construction: Ensures that the chamber retains its vacuum.
- Material Composition: Depending on the process, chambers can be made from metals like steel or other materials that suit various chemical applications.
- View Ports: Allow observation of the processes within without compromising the vacuum.
2.3 Vacuum Gauges
The functionality of vacuum systems is also monitored through vacuum gauges. These devices measure the pressure within the vacuum chamber, ensuring that the desired level of vacuum is achieved and maintained. There are several types of gauges, including:
- Thermocouple Gauges: Use thermal conductivity to measure pressure levels.
- Bourdon Tube Gauges: Mechanical devices that are suitable for rough vacuum applications.
- Capacitance Manometers: Provide precise measurements in high vacuum systems.
3. How Vacuum System Components Work Together
Each component within a vacuum system plays a vital role. Their interaction is crucial to maintaining the system’s overall efficiency.
3.1 The Process Flow
The vacuum pump initiates the process by evacuating air from the vacuum chamber. As the pressure within the chamber drops, the vacuum gauge continuously monitors the pressure levels, providing real-time feedback to operators. This continuous process flow enables businesses to achieve the required vacuum levels needed for specific applications.
3.2 Maintenance and Optimization
Regular maintenance of vacuum system components is crucial for optimal performance. Over time, components can wear out or become inefficient, which can lead to performance issues. Businesses must prioritize maintenance schedules to prolong the lifespan of their systems and ensure consistent operation.
4. Applications of Vacuum Systems
Vacuum systems are utilized in diverse settings, showcasing their versatility and importance. Below are some prominent applications:
4.1 Manufacturing
In the manufacturing sector, vacuum systems are essential for processes such as:
- Packaging: Vacuum sealing extends the shelf life of products.
- Coating: Ensures a uniform deposition of materials on products.
- Forming: The vacuum is used to shape materials through suction.
4.2 Research and Development
In R&D, vacuum systems are integral for experiments that require controlled environments. Applications include:
- Thin Film Deposition: Used in electronic component manufacturing.
- Vacuum Distillation: Allows for the separation of materials based on volatility.
4.3 Food Industry
In the food industry, vacuum packaging is a game changer. It provides preservation by removing air, thus minimizing microbial growth. This application extends to:
- Meat and Fish: Vacuum-sealed products maintain freshness longer.
- Snacks and Dried Foods: Keep items crisp and free from moisture.
5. The Impact of Vacuum System Components on Business Efficiency
The investment in high-quality vacuum system components significantly impacts business efficiency. Here’s how:
5.1 Enhanced Productivity
With efficient vacuum systems, businesses can increase productivity. Automated processes that rely on vacuum technology can minimize downtime, allowing for faster production cycles.
5.2 Improved Product Quality
Vacuum systems help maintain product integrity. By preventing oxidation and contamination, they ensure that the final products meet quality standards and customer expectations.
5.3 Cost Savings
Investing in reliable vacuum systems reduces energy consumption. Efficient systems utilize less power, leading to lower operational costs. Furthermore, effective vacuum systems may reduce material waste, contributing to overall cost savings.
6. Challenges in Vacuum System Operations
Despite the benefits, businesses may face several challenges with vacuum systems:
6.1 Component Failures
As with any mechanical system, component failures can occur. Regular maintenance and monitoring are essential to detect issues early.
6.2 Complexity in Systems
The intricate nature of modern vacuum systems may demand skilled personnel for operation and maintenance, which could lead to additional training requirements.
6.3 Initial Capital Investment
The initial cost of procuring quality vacuum systems can be high. However, the long-term benefits typically far outweigh the initial expenditure.
7. Future Trends in Vacuum Technology
The future of vacuum system components is promising, with technological advancements promising enhanced efficiency and effectiveness. Key trends include:
7.1 Automation
With the rise of Industry 4.0, automation in vacuum systems is becoming standard, allowing for more precise control and operation.
7.2 Energy Efficiency
Advancements in materials and technology will lead to the development of more energy-efficient vacuum systems, further reducing operational costs for businesses.
7.3 Integration with Smart Systems
Smart vacuum systems that are integrated with IoT technology can provide valuable data analytics, helping businesses make informed decisions and optimize processes.
8. Conclusion
Understanding vacuum system components is crucial for businesses across various sectors. By investing in quality components, maintaining them properly, and leveraging advancements in technology, companies can enhance their operational efficiency, improve product quality, and pave the way for sustainable growth. The future of vacuum technology is bright, making it an excellent time for businesses to evaluate and invest in these essential systems.
9. Call to Action
If you’re looking to elevate your business operations with advanced vacuum systems, consider reaching out to industry experts like TMM. They can guide you in selecting the right vacuum system components that suit your specific needs and ensure optimal performance.