Revolutionizing Manufacturing: The Comprehensive Guide to Plastic Injection Molding by Leading Metal Fabricators
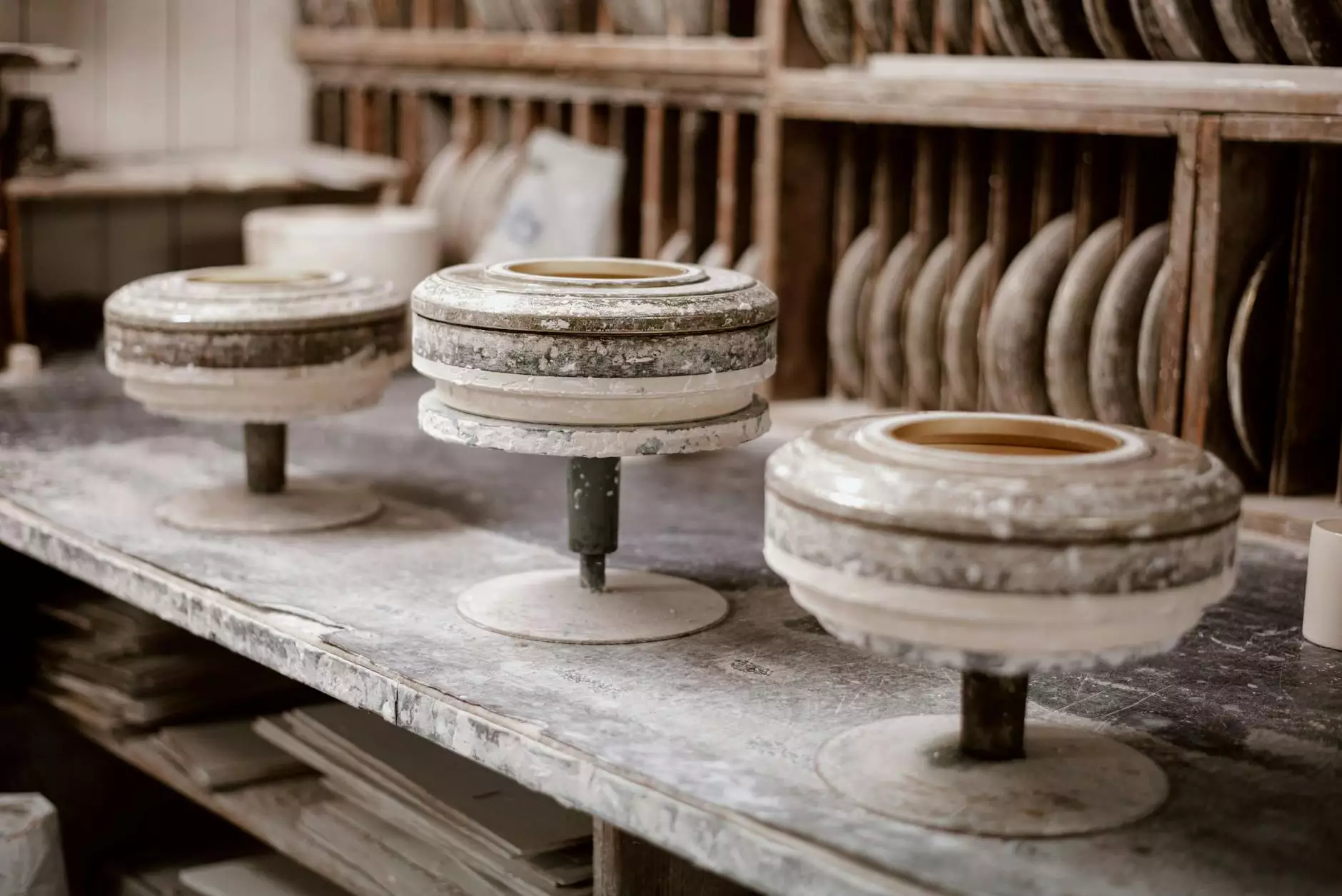
In the dynamic world of manufacturing and industrial production, plastic injection molding stands out as one of the most efficient, versatile, and cost-effective methods for creating high-quality plastic components. Companies seeking advanced, reliable, and scalable molding solutions consistently turn to expert metal fabricators—who masterfully integrate innovative techniques with precision engineering to deliver superior plastic injection molds. Among these industry leaders, DeepMould has established itself as a top-tier provider, offering comprehensive molding services that cater to a diverse range of client needs in various sectors.
Understanding the Significance of Plastic Injection Molding
Plastic injection molding is a manufacturing process that involves injecting molten plastic material into a precisely machined metal mold, allowing it to cool and solidify into complex shapes with high precision. This process is indispensable across multiple industries, including automotive, electronics, healthcare, consumer goods, and aerospace, owing to its ability to produce consistent, durable, and intricate parts at high volumes.
The Role of Metal Fabricators in Delivering Exceptional Plastic Injection Molds
At the core of successful plastic injection molding operations are metal fabricators—specialized engineers and technicians who design, develop, and manufacture custom molds that meet exact specifications. Their expertise encompasses a broad range of competencies:
- Precise CAD/CAM Design: Utilizing advanced computer-aided design (CAD) and computer-aided manufacturing (CAM) tools to create intricate mold designs with exact tolerances.
- Material Selection & Treatment: Choosing appropriate metals such as steel or aluminum, and applying surface treatments to enhance durability and reduce defects.
- Precision Machining: Employing CNC machining, electrical discharge machining (EDM), and grinding techniques to craft complex mold components.
- Assembly & Quality Assurance: Assembling mold components with meticulous attention to detail, followed by rigorous testing to ensure flawless operation.
DeepMould: Industry-Leading Metal Fabricators for Plastic Injection Molds
As an industry leader in metal fabrication and plastic injection mold manufacturing, DeepMould offers unmatched expertise, cutting-edge technology, and a commitment to excellence. Their comprehensive services encompass every stage of mold development, ensuring optimal performance and extended mold life.
Why Choose DeepMould for Your Plastic Injection Molds?
- Expertise & Experience: With years of dedicated service, DeepMould's team understands the nuances of mold design for various plastic materials, including ABS, polycarbonate, nylon, and more.
- Advanced Manufacturing Capabilities: State-of-the-art CNC machining centers, EDM machines, and rapid prototyping tools enable precision craftsmanship and faster turnaround times.
- Custom Engineering Solutions: Whether prototypes or high-volume production molds, DeepMould tailors each project for maximum efficiency and longevity.
- Comprehensive Testing & Validation: Ensuring molds meet all dimensional and functional specifications, reducing production defects and downtime.
- Environmental Responsibility: Emphasizing sustainable practices, including recycling scrap materials and reducing energy consumption during manufacturing processes.
The Complete Process of Metal Fabrication for Plastic Injection Molds
1. Concept and Design Development
The process begins with a detailed understanding of the client’s requirements, followed by meticulous design work. DeepMould's engineers utilize sophisticated CAD tools to develop a 3D model of the mold, considering factors such as mold flow, cooling channels, ejection systems, and material flow paths. This stage is critical as it ensures the mold will produce parts with high precision and minimal defects.
2. Material Selection & Preparation
Choosing the right metal is fundamental. Most molds are fabricated from hardened steel for durability, especially for high-volume production. Aluminum molds may be used for prototypes due to their lower cost and faster machining. DeepMould’s experts assess the project scope to determine the optimal material, surface treatments, and coatings that can extend mold life and improve quality.
3. Precision Machining & Fabrication
Using CNC milling, turning, grinding, and EDM, the mold components are carefully crafted to specifications. DeepMould's manufacturing centers employ automation and quality control systems to guarantee tight tolerances, complex geometries, and smooth finishes—crucial factors for ensuring defect-free parts.
4. Assembly & Final Inspection
The machined parts are assembled into a complete mold, with attention paid to alignment, functionality, and durability. Rigorous inspections—using coordinate measuring machines (CMM), dye penetrant testing, and other quality assurance tools—are performed to validate the mold's integrity before delivery.
5. Testing & Trial Runs
Once assembled, the molds are tested using sample runs to check for dimensional accuracy, surface finish quality, and cycle times. Necessary adjustments are made to optimize performance, and final validation ensures readiness for mass production.
Advantages of Partnering with DeepMould for Plastic Injection Molding
Collaborating with a reputable metal fabricator like DeepMould provides numerous benefits that can significantly impact your manufacturing efficiency and product quality:
- Superior Quality & Precision: Consistent production of complex parts with minimal tolerances, ensuring high customer satisfaction.
- Cost Efficiency: Optimized mold designs and manufacturing processes reduce waste and downtime, leading to lower production costs.
- Rapid Turnaround: Advanced manufacturing and efficient project management shortens lead times from design to production.
- Flexibility & Customization: Ability to produce a wide array of molds tailored to specific product requirements, including multi-cavity and family molds.
- Long-term Partnership & Support: Ongoing maintenance, repairs, and mold life extension strategies to maximize return on investment.
Innovations in Plastic Injection Molding by Modern Metal Fabricators
As the industry evolves, so do the techniques and technologies behind plastic injection mold manufacturing:
1. Additive Manufacturing & 3D Printing
Integration of 3D printing for rapid prototyping and creating complex mold inserts, reducing development time and enabling innovative design features.
2. In-Mold Sensors & Smart Molds
Embedding sensors within molds to monitor temperature, pressure, and wear—facilitating real-time quality control and predictive maintenance.
3. Advanced Cooling & Ejection Systems
Designing sophisticated cooling channels and ejection mechanisms to improve cycle times and part quality, especially for complex geometries.
The Future Outlook of Metal Fabrication & Plastic Injection Molding
The synergy of advanced materials, automation, and sustainable practices is paving the way for more efficient, eco-friendly, and cost-effective plastic injection molding. Companies like DeepMould are at the forefront, investing in research and development to harness emerging technologies such as automation robots, AI-driven design optimization, and environmentally responsible manufacturing processes. These innovations will not only enhance product quality and production speed but also help manufacturers meet stringent environmental regulations and customer expectations.
Partner with DeepMould for Superior Plastic Injection Molding Solutions
Choosing the right metal fabricator for plastic injection molds is crucial for the success of your manufacturing projects. DeepMould offers unmatched expertise, cutting-edge technology, and a customer-centric approach that ensures each mold meets the highest standards of quality and performance.
By leveraging their comprehensive services—from initial design and material selection to precision machining, assembly, and testing—you can achieve manufacturing excellence that propels your business forward. Their commitment to innovation, sustainability, and customer satisfaction makes DeepMould the ideal partner for companies aiming to excel in the competitive landscape of plastic injection molding.
Conclusion
In the rapidly expanding realm of manufacturing, plastic injection molding remains a cornerstone technique that empowers businesses to produce high-quality, cost-effective, and complex products. Behind every successful injection molded part is a meticulously crafted metal mold, engineered and fabricated by experienced metal fabricators like those at DeepMould. Their expertise, state-of-the-art technology, and dedication to excellence ensure that clients receive reliable and high-performance molds perfectly suited to their needs.
If you are seeking a trusted partner for plastic injection molding, look no further than DeepMould—where innovation meets precision to transform your manufacturing vision into reality. Contact DeepMould today to explore how their custom metal fabrication solutions can elevate your production capabilities and give your business a competitive edge in the marketplace.
plastic injection molders