Unlocking the Potential of 3D Printing with PBF Technology
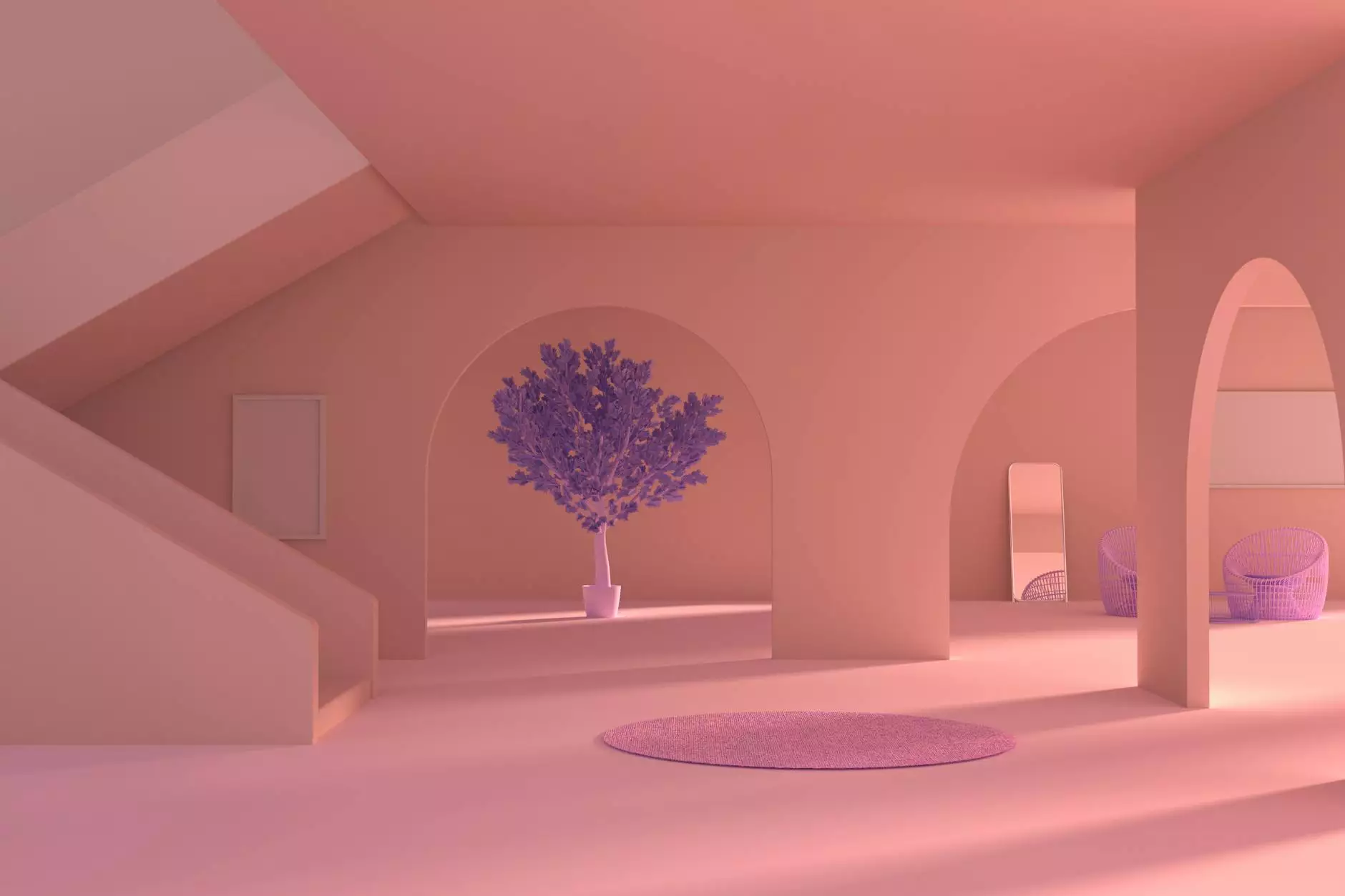
In the ever-evolving landscape of manufacturing and design, 3D printing has emerged as a revolutionary force. Among the many techniques available within this realm, Powder Bed Fusion (PBF) stands out as a particularly transformative approach. This article delves deep into the intricacies of PBF technology, exploring its impacts, advantages, and future in the world of 3D printing, particularly through the lens of Infotron.
What is Powder Bed Fusion (PBF)?
PBF is a unique method of additive manufacturing where powdered material is selectively melted or sintered layer by layer to create solid parts. This technique is applicable to various materials, including plastics, metals, and ceramics, making it a versatile choice for numerous industries.
How Does PBF Work?
The PBF process is innovative yet straightforward. Here’s a breakdown of how it works:
- Preparation: A 3D model is created using CAD software, which serves as the blueprint for the part to be manufactured.
- Layering: A fine layer of powder is spread evenly across the build platform.
- Heating and Sintering: An energy source—typically a laser—fuses the powdered material together following the cross-section defined in the CAD model.
- Repetition: The process is repeated layer by layer until the entire object is completed.
Applications of PBF in Various Sectors
The versatility of PBF technology leads to its widespread adoption across various sectors. Here are some noteworthy applications:
Aerospace
In the aerospace industry, PBF is utilized to manufacture lightweight yet strong components, which are essential for enhancing fuel efficiency and performance. Parts such as brackets, nozzles, and housings are created using PBF due to its ability to produce geometrically complex shapes that were previously unattainable.
Automotive
Automakers leverage PBF to produce prototypes and customized parts quickly. The agility of 3D printing enables rapid iteration of designs, allowing companies to test and refine components without long lead times traditionally associated with machining.
Healthcare
The healthcare sector benefits immensely from PBF technologies, particularly in producing bespoke implants and prosthetics tailored to individual patients. This personalized approach not only enhances patient comfort but also improves overall health outcomes.
Advantages of PBF Technology
Why is PBF gaining such traction within the 3D printing landscape? Here are some compelling advantages:
1. Design Freedom
One of the most significant benefits of PBF is the level of design freedom it offers. Traditional manufacturing methods often impose limitations on design due to tooling constraints. With PBF, intricate geometries and complex features can be achieved without additional costs.
2. Material Efficiency
PBF processes utilize material more efficiently than traditional manufacturing methods. Unused powder can often be recycled and reused, leading to reduced wastage and lower material costs.
3. Speed of Production
When it comes to producing prototypes, PBF is unrivaled in its speed. Parts can be printed in a matter of hours versus weeks for conventional methods, significantly accelerating time-to-market.
4. Reduced Supply Chain Complexity
By enabling local production, PBF diminishes the need for extensive supply chains. This not only cuts costs but also reduces the environmental impact associated with transportation.
Challenges Facing PBF Technology
While PBF technology offers numerous advantages, it is not without its challenges:
1. Surface Quality
Parts produced via PBF may require post-processing to achieve a desired surface finish. This additional step can impede the overall production time.
2. Material Limitations
Although PBF can work with various materials, the range is not as extensive as some other methods. Research and development continue to expand the list of workable materials.
3. Equipment Costs
The initial investment for PBF systems can be quite high, which may deter smaller companies from adopting the technology. However, as the market evolves, these costs are expected to decrease.
The Future of PBF in 3D Printing
The future of PBF technology appears bright, with continuous advancements in materials and processes. As industries strive for efficiency and sustainability, PBF stands poised to meet these demands:
Advancements in Materials
Research into new materials—particularly biomaterials and composite materials—could expand the capabilities of PBF, allowing it to serve even more applications.
Integration with AI and Machine Learning
Using artificial intelligence (AI) and machine learning to optimize PBF processes could lead to further enhancements in speed and quality.
Increased Accessibility
As technology matures, we can anticipate a decrease in equipment costs and increased accessibility for small to medium enterprises, democratizing access to advanced manufacturing techniques.
Conclusion
In conclusion, the role of Powder Bed Fusion (PBF) in the 3D printing ecosystem is undeniably significant. Its capabilities to produce complex designs, enhanced material efficiency, and accelerated production timelines are transforming industries—from aerospace to healthcare. As businesses like Infotron continue to embrace and innovate with PBF technology, the future of manufacturing looks promising and more sustainable.
For companies seeking to stay ahead in the competitive landscape, investing in PBF technology may well be a game-changer, unlocking new opportunities and driving transformative growth.