Enhancing Business Efficiency through Plastic Injection Mold Tooling
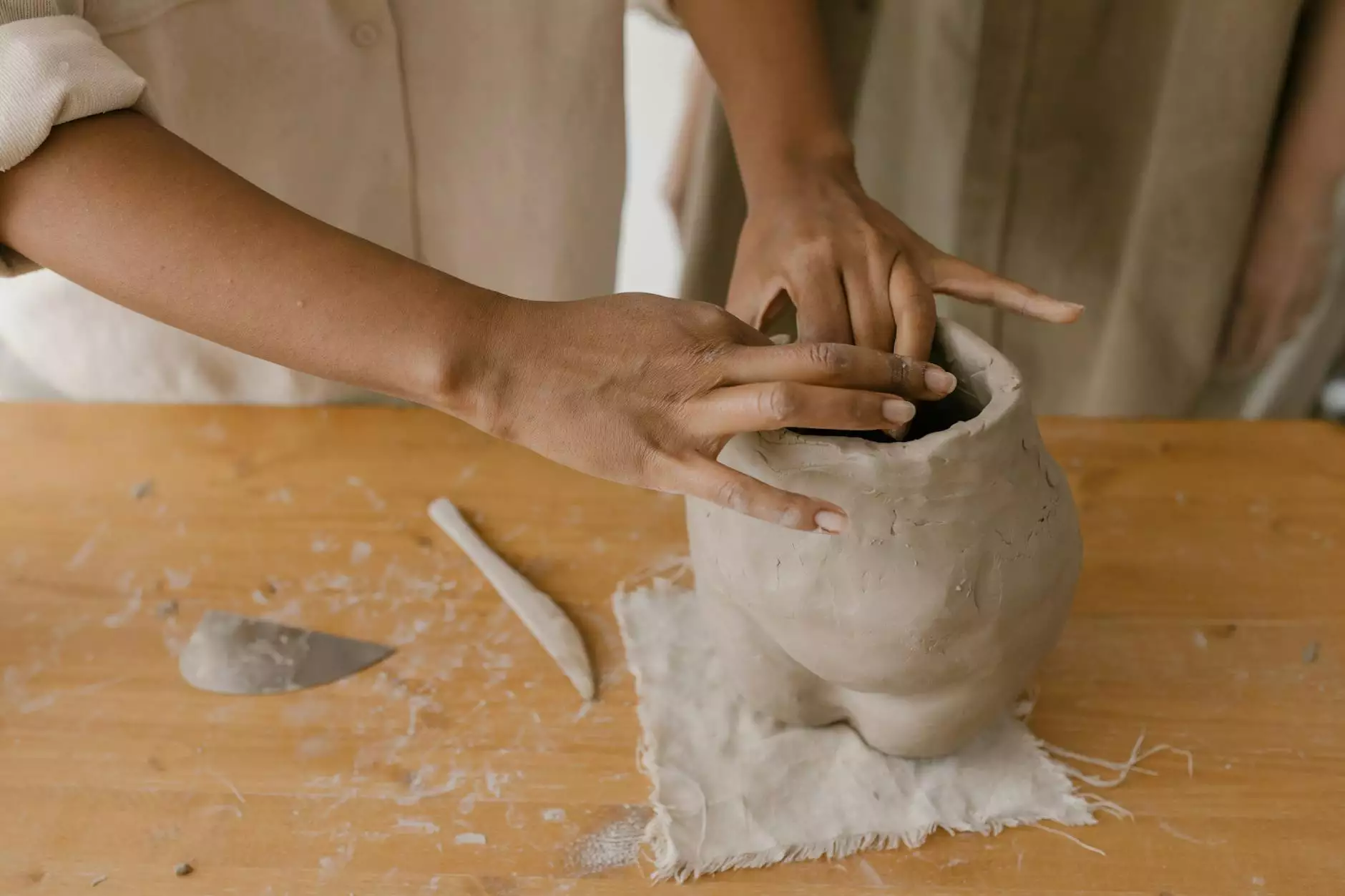
In today's competitive market, optimizing production processes is paramount for businesses seeking growth and sustainability. One of the most effective ways to enhance manufacturing efficiency is through plastic injection mold tooling. This sophisticated process not only improves the quality of products but also accelerates production timelines and reduces costs. In this article, we will delve deep into the realm of plastic injection mold tooling, examining its benefits, processes, and the technology driving its success.
Understanding Plastic Injection Mold Tooling
Plastic injection mold tooling refers to the process through which molten plastic is injected into a mold to create parts and products. This method is widely used in various industries, from automotive to consumer goods, because of its remarkable precision and efficiency. The process ensures minimal waste of material, high reproducibility, and cost-effectiveness, making it a cornerstone of modern manufacturing.
The Components of Plastic Injection Mold Tooling
- Mold Design: The mold is custom-designed to create specific parts. It consists of two halves that come together to form a cavity where the molten plastic is injected.
- Injection Machine: This machine melts the plastic material and injects it into the mold under high pressure.
- Cooling System: Once the plastic is injected, it needs to cool and solidify. The cooling system is essential for maintaining the desired shape and dimensions.
- Ejection System: After the part has cooled and hardened, it must be ejected from the mold. An effective ejection system ensures smooth removal without damaging the product.
Benefits of Plastic Injection Mold Tooling
Utilizing plastic injection mold tooling can bring numerous advantages to a business, some of which include:
1. Cost Efficiency
One of the primary benefits of plastic injection mold tooling is its ability to minimize production costs, particularly when producing large volumes of items. The initial investment in molds and machines may be significant, but the cost per unit decreases substantially with increased production runs.
2. Design Flexibility
Modern injection molding allows for intricate and complex designs that may be challenging or impossible to achieve with other manufacturing processes. This flexibility supports innovation and creativity in product design, leading to unique offerings in the marketplace.
3. High Precision
The technology behind plastic injection mold tooling allows for incredible precision in manufacturing. Parts produced through this method are often within tight tolerances, ensuring a high degree of consistency between units.
4. Quick Production Time
With the ability to produce thousands of parts in a single cycle, plastic injection molding significantly reduces the time required for production. This rapid output is crucial in industries where speed to market is a competitive advantage.
5. Waste Reduction
Efficient use of materials is another hallmark of injection molding. Closed-loop systems and precise control over the injection process mean waste is minimized, contributing to more sustainable manufacturing practices.
Applications of Plastic Injection Mold Tooling
The versatility of plastic injection mold tooling spans various sectors, showcasing its adaptability and wide application. Here are some key industries where this technology is prominently utilized:
1. Automotive Industry
In the automotive sector, injection molding is used to create interior and exterior components, such as dashboards, trim pieces, and even engine parts. The ability to produce complex shapes and structures means that manufacturers can develop lighter and more efficient vehicles.
2. Consumer Electronics
From smartphone cases to internal components of gadgets, the consumer electronics industry relies heavily on plastic injection molding to produce durable and lightweight products that enhance user experience while keeping costs manageable.
3. Medical Devices
The production of medical devices often requires compliance with strict regulations regarding safety and reliability. Plastic injection molding can provide the precision and consistency needed to manufacture components like syringes, surgical instruments, and housings for electronic medical devices.
4. Furniture and Home Goods
Injection molding is also prevalent in producing household items and furniture components, including chairs, tables, and storage solutions. The ability to create ergonomic designs with varying materials allows for a diverse range of products.
The Future of Plastic Injection Mold Tooling
As technology continues to evolve, so does the potential for plastic injection mold tooling. Innovations in materials, process automation, and artificial intelligence are poised to revolutionize how products are designed and manufactured.
1. Sustainable Practices
With an increasing emphasis on sustainability, the future of injection molding will likely involve more eco-friendly materials and processes. Bioplastics and recycled materials are gaining traction, allowing manufacturers to reduce their environmental footprints.
2. Automation and Industry 4.0
The integration of IoT and automation in manufacturing processes is set to enhance operational efficiency. Smart factories will utilize data analytics and machine learning to optimize production schedules, reduce waste, and improve product quality.
3. Advances in Materials Science
Ongoing research in materials science is yielding new types of plastics that are stronger, lighter, and more durable. These developments will expand the capabilities of injection molding, broadening its applications across different industries.
Choosing the Right Partner for Your Plastic Injection Mold Tooling Needs
When considering plastic injection mold tooling, partnering with a reputable manufacturer is essential. A reliable partner will not only provide high-quality tooling and production but also support you from the design stage through to the final product.
Factors to Consider:
- Experience and Expertise: Look for a provider with a proven track record in your industry and extensive experience in mold design and manufacturing.
- Technological Capabilities: Evaluate their access to modern technologies and equipment, including CAD/CAM systems and automated processes.
- Quality Assurance: Ensure that the partner adheres to stringent quality control measures and certifications.
- Customer Support: Good communication and support throughout the project lifecycle are vital for addressing potential issues and ensuring timely delivery.
Conclusion
In conclusion, plastic injection mold tooling represents a hallmark of modern manufacturing that significantly enhances business operations across various industries. By adopting this technology, companies can streamline their production processes, reduce costs, and produce high-quality products. As the industry continues to innovate, the potential for injection molding will only grow, making it a wise investment for businesses looking to remain competitive in an ever-changing market.
To explore your options in plastic injection mold tooling and discover how it can benefit your business, consider reaching out to expert manufacturers like Deep Mould at deepmould.net. With their expertise in metal fabricators and commitment to quality, they can help you unlock the full potential of your manufacturing capabilities.